Industrial Robotics Repair
ACS Repairs Robotics Electronics
and Repair Quote
ACS is here for you! Having expert robotics repair technicians at the ready for your robotics and automation maintenance and repair needs will save you time and money. Our Tech Team has experience with many robotics and automation systems from warehouse robot repairs to cobots and most everything in between.
- SAVE - Repair and save up to 70% of the cost to purchase a new one
- FAST TURNAROUND - Most repairs are back in your hands in about 3 weeks, with our Rush Repair Service shipping in just 3-5 days
- FULL WARRANTY - We Guarantee Our Repairs With A Full Two-Year Warranty
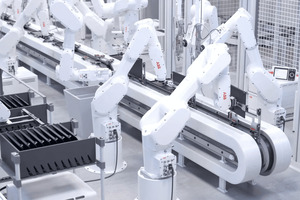
ACS Repairs ABB Robot Electronics.
The ACS customer service team is unparalleled in the industry – our knowledgeable and helpful service team answers live during business hours to provide you with the level of information and communication that you and your company need. We are ready to service all of your industrial electronic robotics needs!
The following is a list of the most popular manufacturers we service and repair. If your manufacturer is not shown here, it is very likely we can be of assistance. Just contact us for more information using our Contact page, or call 800-605-6419.
- ABB
- ASI Robotics
- Fanuc
- Kuka
- Mitsubishi
- Motoman
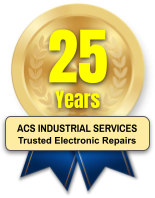
- All you pay is shipping.
- No Estimates - No Surprises ... Accurate Quote within 72 hours.
- Replace or Repair? Why Guess ... send us your item and then decide.
It may be clear when you are in need of robot repair, but this shouldn’t be the only time you maintain your company’s robotics. When it comes to industrial robots, preventative maintenance is critical. Why wait until something goes wrong with them and your production comes to a stop?
There are many reasons to prioritize preventative maintenance for robotic systems. Some of the most significant benefits of preventative maintenance include:
- Early detection: First, preventative maintenance allows you to identify potential issues with industrial robots before they become big repair problems. Noticing a part is about to wear out during a basic maintenance check and quickly replacing it is much cheaper and easier than waiting for that part to fail, possibly taking down other parts of the robot at the same time.
- Longevity: Preventative maintenance for industrial robots also allows you to extend the life of those robots dramatically. Over time, stresses can add up and put an end to the robot’s life span far too early.
- Efficiency: Well-maintained machines also tend to operate more efficiently giving you good value for the money you spent on the robotic system.
- Control: By doing regular preventative maintenance, you control how a robot’s repairs will affect your business. If a maintenance check reveals a problem, your company can solve the problem in stages, or fix it at a time when the robot would normally not be in operation or can have its duties replaced by another robot. This means you can dramatically reduce or eliminate downtime, preserving your productivity. Contrast that with your whole production line grinding to a halt unexpectedly.
- Cost savings: Generally, preventative maintenance tasks are more affordable than emergency repairs in the case of a breakdown. Your business can also save money by avoiding unplanned downtime and keeping your operations in full swing.
Our Customers Say

Just wanted to drop you a line and thank you and your staff for doing a great job. I am very pleased and I will pass your services on to other plasma cam owners. Thanks Again.
Business Owner
Galva IL
